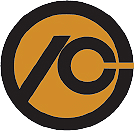
Material Handling System
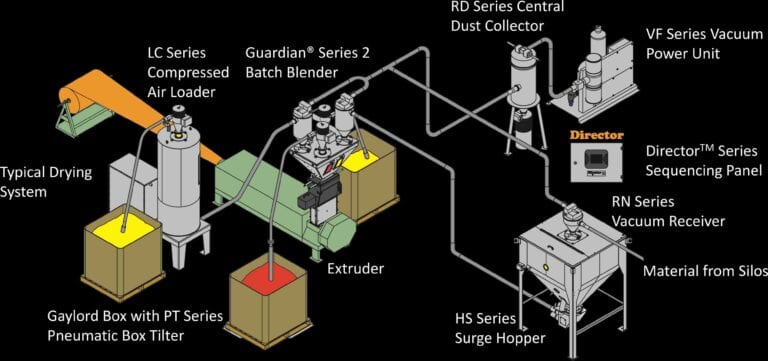
VF Series Vacuum Pump
The VF Series is PCC’s most popular line of vacuum power units, offering dependable and economical performance for a wide variety of conveying rates, distances and materials. Typical applications include in-plant distribution systems and machine/blender loading. Each system is carefully sized using PCC’s computer calculations to meet your conveying specifications.
Standard features include motor size range from 2.2 to 22 KW (3 to 30 HP), positive displacement blower, ย enclosed V-belt drive, ย single element paper filter assembly,ย T-frame TEFC motors that are suitable for both indoor or outdoor usage, ย discharge silencer, vacuum relief valve and gauge and motor starter panel.ย Optional features include ย power saving variable speed drive controlled by the Directorโข Series sequencing control panel, ย customย voltages, ย continuous run valve to reduce pump cycling, sound-deadening enclosures and construction for outdoor placement.
EMV Variable Speed Drive for Vacuum Power Units
Process Control’s EMV variable speed drive for VF series vacuum pumps have the ability to slow down or speed up the pump to match the conveying requirements for each vacuum receiver station. By controlling the speed, no only does the drive allow the user to save energy, but it helps keep the material undamaged during the conveying process. This upgrade reduces dust, angle hair and snake skin generated by transporting pellets too quickly or too slowly through material transfer lines. The conveying speeds are easily controlled with theย Directorโข Series sequencing control panel. The VSD can be included on new systems for as a retrofit to existing systems. Significant government funded rebates are available in many jurisdictions to encourage adoption of this energy saving upgrade.
VB Series Vacuum Pump
The VB Series from Process Control is designed for low to moderate rate conveying and quiet, low-maintenance performance. As ย part of an integrated material handling system, the VB Series can improve the efficiency of your plastics processing. Standard motor is 460V/3PH/60Hz with options for custom voltages. Control voltage is 24VDC or 115 VAC.
Standard features include motor size range from 2.2 to 5.6 KW (3 to 7.5 HP), quiet ring compressor design,ย TEFC motor for indoor usage only, ย dual-stage intake filter, vacuum relief valve andย motor starter panel.ย Optional features includeย power saving variable speed drive controlled by the Directorโข Series sequencing control panel andย continuous run valve to reduce pump cycling.ย
RD Series Central Dust Collector
As part of Process Control’s Material Handling System, the RD Dust Collector is the ideal solution for dust removal on the vacuum line of a system. With the timed self-cleaning, it keeps the line free of any possible fines associated with pellets or regrind material with minimal operator intervention. The cleaning system is operated by the Directorโข Series sequencing controller to properly back flush the bags. Various filter bags are available for anything from coarse to extremely fine dust. The filter bags can be easily replaced or cleaned as needed. Once the back flush cleaning system is done, dust is dropped into a bucket for easy removal. Available with AC or DC solenoids.ย
Standard features include filter bags, V band clamp, dual solenoid sequencing T (performs cleaning), ย flapper valve material exit, built-in stand and easily removable dust collection bucket.
Directorโข Series Sequencing Control Panel
The Directorโข Series sequencing control panel is an easy-to-use touch screen panel that allows operators the ability to control and monitor all aspects of a central vacuum loading system. The sequencing panel controls the central vacuum pump, the vacuum receivers and can also control a central dust collector and a continuous run valve.ย All information and operating controls of the Directorโข are located on a touch screen interface. The touch screen interface allows the user to activate, adjust and monitor loading and system information on the panel.
Most features on the user interface are self-explanatory, but a HELP key is located on every screen to further assist with operational procedures.ย System configurations can be specified to load from 4 to 30 stations using one or more pumps. Other configurations can also be defined based on the requirements of the system. The entire system has been intuitively mapped giving the user benefits in both technology and process control.
Standard features include ย Allen Bradley MicroLogixโข 1400 PLC with Ethernet port, ย 150 mm (6 inch) colour touch screen, ย displays alarm conditions and maintains alarm log, automatic fill time calculation, status or progress monitor.ย Optional features include 250 mm (10 inch) colour touch screen, multiple pump, dust collector control, special controls andย electrical specifications, variable speed pump control for each station, remote panel and ย remote communication capability via Ethernet/IP, DeviceNet or DH485.
RN Series Vacuum Receiver for Pellets
The RN Series Vacuum Receiver is designed to be mounted at any point where resin delivery is needed. Material flow from the connected source is operated by the Directorโข Series sequencing control panel. When full, the flapper valve opens to dump the contents into the material hopper or it is held for future use by a positive shutoff valve.ย A built-in screen prevents carry-over of pellet material back to the vacuum pump. A drawer screen allows convenient access to the filter for cleaning. The RN Series Vacuum Receiver is low-maintenance. No valves come into contact with conveyed material and no tools are needed for pellet retaining screen changes. Total compressed air requirement ย is 0.14 dm3ย (0.005ย ft3) per cycle. Working capacity range is from 2 to 85 dm3ย (0.07 to 3.0ย ft3).
Standard features include compressed air operated sequencing valve for solenoid actuators and control cylinders,ย 24 VDC control voltage, load level proximity switch, flapper-type valve to create a positive seal, simple slide-out pellet screen with two side latches and mild steel construction.ย Optional features include check valve for common material line applications, swing-gate or knife-gate positive shut-off discharge valve,ย 110VAC control voltage, stainless steel construction, Directorโขย series sequencing control panel, central vacuum power unit, central dust collector and high temperature design.
RP Series Vacuum Receiver for Dusty Materials
The RP Series self-cleaning action avoids carry-over of dust back to the vacuum power unit by back flushing the filters at programmable cycle intervals thatย is controlled by the Directorโข Series sequencing control panel. Dislodged fines are dropped back into the hopper. The filter bags in the RP Series feature large filter areas to promote low, stable pressure drop. No valves come into contact with conveyed material and no tools are needed for filter cleaning or changes.ย No plant compressed air is used for cleaning. Total compressed air requirement ย is 0.28 dm3ย (0.01ย ft3) per cycle. Working capacity range is from 11 to 89 dm3ย (0.4 to 3.14 ft3).
Standard features include ย compressed air operated sequencing valve in lid for solenoid actuators and control cylinders, internal self-cleaning filter bags for granular or dusty materials,ย 24 VDC control voltage, flapper-type discharge valve with magnetic switch, removable lid with V-band clamp and mild steel construction.ย Optional features include check valve for common material line applications, swing-gate or knife-gate positive shut-off discharge valve,ย 110VAC control voltage, stainless steel construction, load level proximity switch, pre-wired junction box to simplify installation and high temperature design.
LC Series Self Contained Compressed Air Loader
The LC Series assembly is space efficient, self-contained unit which uses compressed air to convey materials from 60 to ย 385 kg/hr (130 to 850 lb/hr). The ย high efficiency cyclonic hopper is mounted on a clear view tube with mounting flange, an air-flow amplifier, an exhaust air filter, and control box. Loading is controlled by a proximity sensor mounted in the view tube. All components are attached directly to the unit, making installation fast and simple. An aspirated pickup wand and 3 meter (10 ft) of PVC flex hose is included for pulling raw material from Gaylord boxes or storage bins.
Standard features include clear view material outlet tube mounting flange; easily accessible, top-mounted air discharge filter ย load level proximity sensor,ย compressed air operated venturi, ย power supplied as 115V/1PH/60Hz or 230V/1PH/50Hz and mild steel construction.ย Optional features include custom mounting adapter, stainless steel construction and dual inlet for proportional loading of pellets and regrinds. This feature brings both material in simultaneously to eliminate layering. The percentages are set by adjusting the air pressure settings.
HS Series Surge Hopper
The HS Series surge hoppers are ideal for in-plant storage of both raw materials and finished product. Available in a variety of sizes and capacities to maximize and conserve handling time space and energy. Capacity range is 0.85 to 8.2ย m3ย (30 to 290ย ft3), depending on the model selected. Hoppers are available withย slopes of 45ยฐ, 60ยฐ or 70ยฐ for difficult flow materials.
Standard features include, high and low level view windows, lifting lugs for easy placement, bolt down foot pads, heavy duty angle iron legs and reinforcement bracing, hinged top cover for easy access, lid configured for mounting vacuum receiver or cyclone and mild steel construction.ย Optional features include bridge breaker for difficult flow materials; manual or automatically operated slide gate discharge valve, vacuum take-away box and aspirated outlet stubs, drain tube for discharging directly into gaylord boxes or drums, leg extension for gaylord box clearance, high and low level proximity or rotary sensors, epoxy coated interiour, custom paint colour and stainless steel construction.
PCC Process Manager
ย ย ย ย SCADA Total Integration Services includes a process visualization software package. The key advantages are:
- Automatic data acquisition and storage.
- Centralized control or monitoring multiple blenders from one location.
- Ability to distribute data to PC desktop, signage display, handheld tablet for corporate MES/ERP system.
Features include::
- Default configuration is for monitoring and controlling (1) PCC Continuous Blender, (1) PCC Batch Blender, or (1) PCC Gravitrol weigh hopper (with B&R Touchscreen, or Mini-Op equipped with Ethernet capability).
- Virtually limitless expansion of the SCADA system to additional PCC and non-PCC equipment, configured by PCC technicians.
- Includes one runtime version of Siemens WinCC software with SQL server, one license (for one computer only).
- Functions include real time blender operations (both monitor and control), material usage, historical trending, and alarm logging/notifications, all from one centralized location.
- Inventory trends and summary reporting can be exported to any spreadsheet program, such as Excel.
- Operator and Supervisory levels, with multiple security settings available.
- Requires PC with WindowsTM OS 7 or 10 to operate software.